Intervista Giulio Dal Lin
"L’idea alla base è stata quella di adottare l’approccio Lean in “toto” [...] e mettere le basi per una cultura dell’eccellenza."
Quando si è cominciato a parlare di Lean in CAREL?
Il primo contatto con i principi e le tecniche del Lean Thinking risale al 1994, quando il Presidente di CAREL, Luigi Rossi Luciani, prese parte ai primi seminari in Veneto circa la filosofia Lean e la sua applicabilità al sistema industriale veneto. Ai workshop, della durata di 6 mesi con cadenza settimanale, partecipavano le massime competenze universitarie sul tema quali il Prof. De Toni, il Prof. Filippini, il Prof. Forza e il Prof. Vinelli e un piccolo numero di imprenditori interessati. Da quel momento è nato il desiderio di trasformare CAREL in un’azienda Lean.
In parallelo al corso, Rossi decise di indire delle riunioni settimanali con un gruppo di manager, seguendo uno schema originale: ogni manager doveva commentare, a turno, un capitolo del libro "La macchina che ha cambiato il mondo". Un metodo efficace, per introdurre i concetti Lean in CAREL.
Quanto tempo ci è voluto per strutturare la Lean in CAREL?
La trasformazione è iniziata qualche anno dopo, a partire dalla fine del 2006; l’idea alla base è stata quella di adottare l’approccio Lean in "toto", non limitandosi cioè solo a un’applicazione estemporanea di strumenti e tecniche, ma piuttosto intraprendendo una trasformazione dell’azienda che portasse anche a un cambiamento della cultura, dei comportamenti, del modo di lavorare insieme. Qualcosa che potesse cioè durare nel tempo e potesse mettere le basi per la cultura dell’eccellenza. Occorreva il coinvolgimento di tutti i livelli, attraverso la comprensione del perché si volesse andare in questa direzione, promuovendo un cambiamento a piccoli passi, ma costante. Sono emersi in modo evidente valori quali spirito di squadra, il voler migliorare i processi esistenti attraverso la riduzione degli sprechi, la visibilità e la trasparenza delle azioni, la necessità di abbattere le barriere di comunicazione, il desiderio di portare il valore per il cliente al centro delle discussioni. Sicuramente, anche la convinzione di non "adagiarsi" sui risultati positivi, ma di voler essere in costante "mutazione" per garantire crescita e sviluppo dell’organizzazione a fronte di un mercato sempre più competitivo.
Quali sono stati i principali ostacoli?
Il primo ostacolo, se così si può chiamare, è stato quello che CAREL in quel momento storico fosse un’azienda di successo, senza l’evidente necessità di dover intraprendere una qualsiasi trasformazione. Fatturato solido, forte crescita, clienti in generale soddisfatti. C'era però qualche segnale debole che dava avvisaglia della necessità di "fare qualcosa". In primis, la crescita aveva portato a un’organizzazione sempre più articolata e strutturata, con il rischio di creazione di potenziali "silos" organizzativi meno collegati e aperti rispetto al passato. Poi la complessità crescente stava portando a un generale aumento dei lead times di processo, ad esempio dei tempi di produzione e dei tempi di sviluppo prodotto. C’era anche in generale difficoltà nel coordinamento di iniziative complesse e si sentiva la mancanza di trasparenza e visibilità delle azioni dei team di lavoro. C'era anche bisogno di lavorare sulla diffusione della strategia aziendale e sul collegamento poi alla parte esecutiva. Tutti segnali che, guardati rispetto ai risultati, sarebbero sembrati "parte del gioco", ma che agli occhi attenti della proprietà erano importanti suggerimenti da cogliere per non rimanere fermi e iniziare a fare qualcosa in ottica "snella".
"C’era anche bisogno di lavorare sulla diffusione della strategia aziendale e sul collegamento poi alla parte esecutiva."
Quali dipartimenti/uffici sono stati coinvolti per primi?
Le organizzazioni in cui è partita la trasformazione sono state R&D e Operations. In R&D, c'era l'esigenza di aiutare i colleghi a migliorare il processo di sviluppo prodotto, la collaborazione reciproca e l'organizzazione stessa del lavoro. Era infatti presente una certa complessità nel gestire i progetti e questi stavano assumendo complessità crescente, sia in termini di task da compiere che di persone coinvolte. Molte persone poi lavoravano su più progetti allo stesso tempo, disperdendo quindi focus ed energie. Il risultato era un allungamento dei tempi di progetto e a volte qualche problema di qualità. Sono nati così i concetti di team compatto, del visible planning, del "one project flow" similare al concetto del one piece flow produttivo. Grazie a questo approccio, si sono ridotti drasticamente i ritardi di progetto.
In Operations, invece, il motore cardine del cambiamento è stato il tema della creazione del "flusso di valore": si è passati da una logica di reparti produttivi e meccanismi di batch & queue, alla creazione delle Value Stream e dell’organizzazione a supporto della Value Stream stessa che risiede nel gemba, vicino alle linee produttive. Il concetto di One Piece Flow è stato fondamentale per supportare il business model di CAREL: produzione su nicchie rilevanti anche di piccole quantità per assecondare le esigenze dei clienti. Per esempio si sono sviluppate isole di lavoro basate su un miglioramento significativo dell'ergonomia.
In tutte le aree, sono stati introdotti i "Lean basics": PDCA, visible planning, 5S; questo è un fattore essenziale per garantire partecipazione, coinvolgimento e contributo da parte di tutta l'organizzazione. La Lean, in Operations, ha permesso di migliorare indicatori di sicurezza, qualità, rispetto delle consegne e costi.
Quand'è iniziata la condivisione della filosofia con le filiali, e quali sono state le filiali coinvolte per prime? Come hanno accolto questo cambiamento?
Il coinvolgimento delle filiali è iniziato verso il 2013, seguendo il principio di voler estendere i benefici portati dall'introduzione del Lean thinking a tutte le organizzazioni del Gruppo. Le filiali rappresentano un tassello importantissimo in questo senso, in quanto hanno un contatto privilegiato con i clienti e sono molto vicine alle esigenze del mercato.
Le prime coinvolte sono state quelle europee, a partire da CAREL Deutschland per poi arrivare al coinvolgimento di quelle extra europee, in particolare di quelle asiatiche ed americane. Il principio guida del lavoro sulle filiali è molteplice: semplificare i processi interni portando visibilità sul flusso dell’ordine e sui KPIs critici di performance per i clienti, coinvolgendo le varie funzioni della filiale stessa; introdurre concetti Lean come il PDCA per poter contare sul contributo esteso di tutti in termini di miglioramento continuo e innovazione; strutturare dei progetti di miglioramento in tutti i processi di interazione tra filiali e tra filiali ed HQ, in cui sappiamo esserci molte possibilità di semplificazione e miglioramento data la forte crescita che caratterizza la nostra Azienda.
Oggi, quante sono le persone che si occupano di Lean in tutto il gruppo?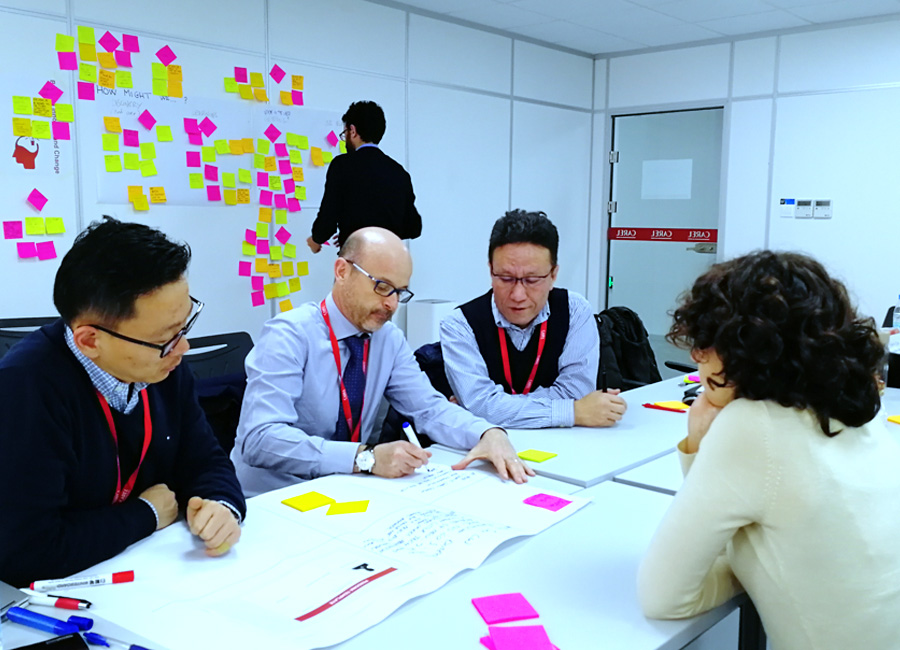
Circa 2000… è la nostra missione!
Far sì cioè che ogni persona che lavora in CAREL possa applicare nel quotidiano e nel suo lavoro i principi e i valori del miglioramento continuo.
In quest'ottica, è nato un paio di anni fa il ruolo di Lean Ambassador, un ruolo "part time" aperto a tutti quei collaboratori che volessero partecipare attivamente allo sviluppo del programma Lean dell'Azienda.
A livello di organizzazione Lean abbiamo invece una struttura di circa 15 persone in tutto il gruppo, persone che lavorano full time in ambito Lean e che seguono progetti e le diverse organizzazioni.
Oggi il Lean department rappresenta il centro di competenza per:
Miglioramento continuo (Lean + six sigma)
Processi di Innovazione (incluso Business Model Generation, Design Thinking…)
Project management
Formazione Lean
Hoshin Kanri
Qual è il futuro della Lean in CAREL?
La Lean, in CAREL, ha esteso oggi il proprio ambito di azione e competenza e si sta "aggiornando" alla luce delle nuove necessità interne, sfide di mercato e trend di innovazione esterna. Innanzitutto, si occupa sempre della Lean "tradizionale", intesa come principi, strumenti e metodi che derivano dal Toyota Production System e dal mondo Lean di Womack, Jones, & co.
Questo è un aspetto da non sottovalutare: i principi base Lean sono "semplici", ma "potenti" per garantire crescita e stabilità. È quindi fondamentale costantemente rivedere e fare "manutenzione" ai nostri processi.
Poi è stato introdotto recentemente il tema della process innovation e della business innovation (abbiamo anche modificato in tal senso il nome dell'ufficio). Qui abbiamo abbracciato approcci di Design Thinking e Business Model Generation. Recentemente, il tutto poi ha avuto una forte spinta muovendo i primi passi sul tema Agile e Scrum, con anche la certificazione dei primi Scrum Master e Product Owner interni.
L'ufficio Lean poi oggigiorno ha una competenza sempre più spinta in ambito project management, fatto che ci vede alla guida di alcuni progetti strategici aziendali. L'altra sfida è il mondo post M&A, quindi il lavoro su uno standard sul tema acquisizioni e su come poi coniugare la rivoluzione dettata dall'Industry 4.0 o ormai 5.0 ed i principi Lean.
Non manca certo la varietà!